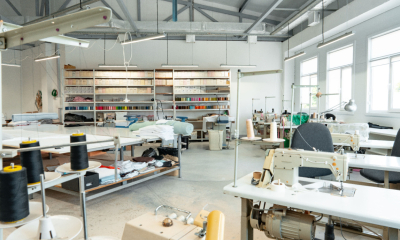
Managing a factory's energy demand has become crucial to long-term profitability, given the rising costs of energy as the increasing awareness of environmental conservation. However, many organisations struggle to manage the relationship between energy conservation and output, with the latter often taking a toll on the former.
What if, however, you had both? Imagine a factory in which prices are reduced, energy usage is kept to a minimum in accordance with energy saving strategies, and production lines operate precisely. Striking this balance is actually completely doable - all it takes is the implementation of appropriate tactics as suggested by Utility Bidder.
In this article, you will learn how to achieve maximum value for your business by looking at the five most effective ways to make your premises more energy efficient, ranging from small improvements to radical innovations.
Strategy 1: Energy audit to establish inefficiencies
The first step to improving your energy efficiency is to conduct an energy audit. Some areas of your factory may be clearly inefficient. For example, outdated lighting installations, dysfunctional HVAC systems or areas of the building lacking proper insulation.
This can help you reduce energy costs, manage energy utilisation, and makes your business more environmentally friendly. Conduct research to identify areas of inefficiency in your factory.
Strategy 2: Optimising lighting systems
Production line activities commence as the lights go on and the machines swing into operation. Every factory needs lighting so that production line workers can carry out their work.
However, with typical lighting systems being responsible for up to 40% of a factory's energy budget, they can be a major source of energy wastage.
Optimisation of lighting systems is often the first stage when looking to improve the energy efficiency in any building. To minimise energy wastage you can install smart systems such as sensors and timers for controlling lighting systems.
Strategy 3: Rehabilitation of energy-intensive motors and drives
Every factory requires industrial motors and drives to propel equipment and enable the smooth running of the business. However, older and more inefficient drives and motors will drain energy at a much faster rate.
You could free up a powerful energy saving and increase your factory's productivity by using more energy-efficient motors and drives. Modern motors and drives are often far more efficient and can minimise the energy loss through heat by employing the latest technology.
What's the outcome? Reduced energy consumption, lower utility costs and reduced impact on the environment.
Strategy 4: Delay the onset of maintenance using predictive maintenance programmes
In any manufacturing environment, timing is essential. Losses, such as those posed by downtime, could be catastrophic. Whenever there's a breakdown in equipment, manufacturing lines are affected and a lot of time and money is wasted.
An effective program that implements the concept of predictive maintenance would be helpful. With IoT sensors, AI technology, and machine learning, you may begin to identify early signs that some of your equipment is about to fail. This allows you to plan for its service at a time when the production line is not fully active or during off-peak production.
This prophylactic approach is effective not only in reducing the occurrence of unexpected downtime but also in increasing the equipment's operational time, reducing repair costs, and creating optimal maintenance strategies.
Strategy 5: Ensure the building is well insulated to reduce heat loss
It's easy to ignore the impact of heat loss on energy efficiency when you're in the middle of a busy production facility.
However, neglecting this important detail can result in a significant drain on your finances, as well as a significant rise in energy costs.
Therefore, increasing insulation and minimising heat loss are essential for boosting the energy efficiency of manufacturing. You might be able to successfully plug these energy leaks to ensure that your factory retains warmth and uses its energy more efficiently.
Conclusion
It's evident that there are many options for boosting productivity and energy efficiency.
These five techniques will help lower your energy costs and usage and open the door to a more productive, sustainable, and efficient factory floor.
You can boost your operations at every stage by maximising the efficiency of your HVAC and lighting systems by utilising data analytics and staff involvement.
These measures for utilising energy will enable you to shift your focus and direct resources towards innovation, expansion, and improved profitability.
Manufacturing holds a very promising position for itself in the future, and these techniques will guide you towards it.
Copyright 2024. Featured post made possible by Kallia Stergianos, Utility Bidder.